Understanding Custom Injection Molding Companies
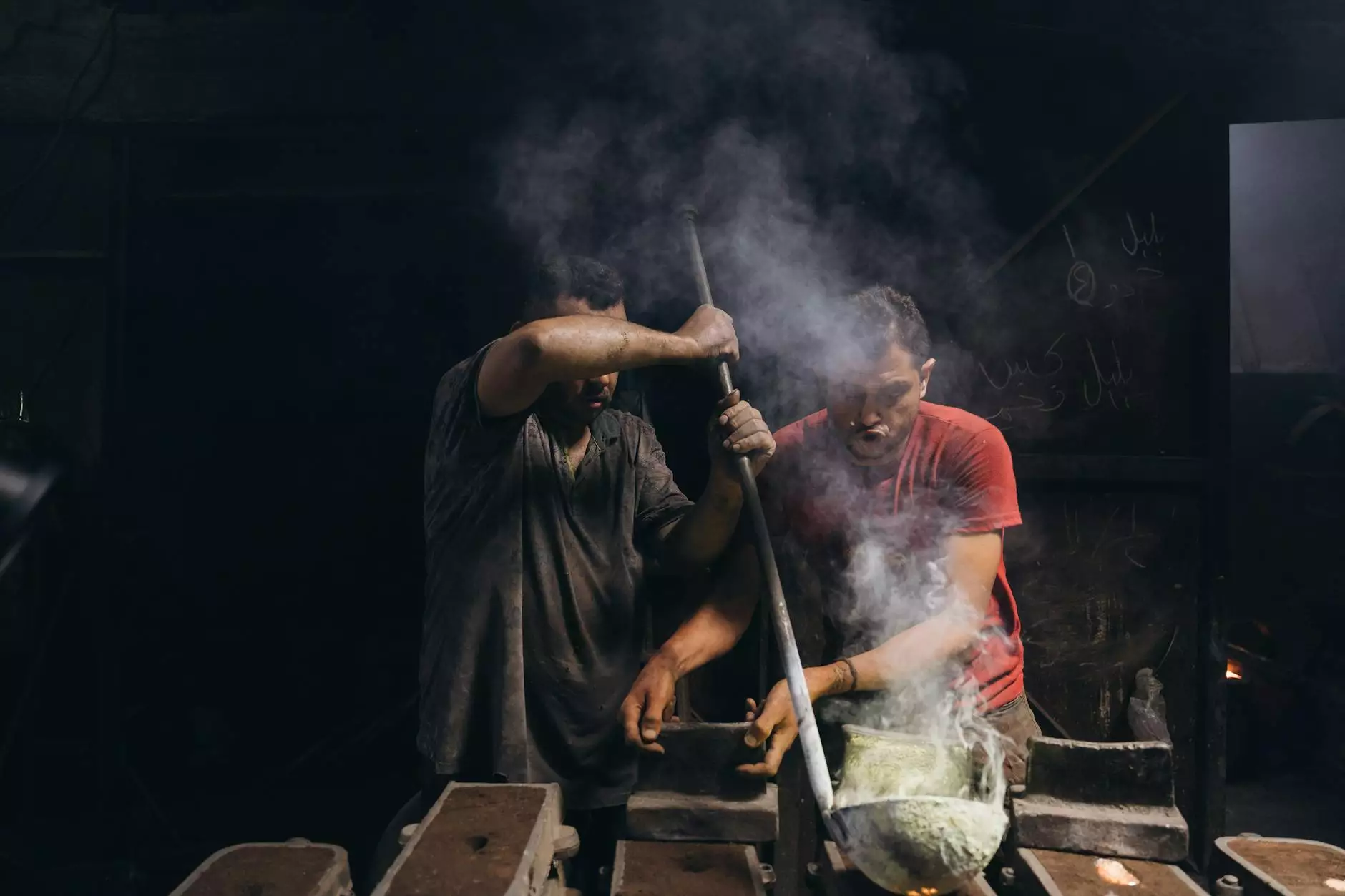
Custom injection molding companies have become vital to modern manufacturing, providing businesses with the ability to produce complex shapes and high-density products efficiently and cost-effectively. In this comprehensive article, we will delve into what custom injection molding entails, the benefits it offers, and the various factors to consider when selecting a partner for your manufacturing needs.
The Basics of Custom Injection Molding
Injection molding is a manufacturing process that consists of injecting molten material into a mold to create a specific shape. Often utilized for producing plastic parts, this method allows manufacturers to produce high volumes of identical components with incredible precision. Here are the fundamental steps in the injection molding process:
- Material Selection: Typically, thermoplastics or thermosetting polymers are used, chosen based on the application's requirements.
- Mold Design: This step involves creating a mold that can withstand high pressure and temperatures, designed to form the desired shape of the final product.
- Injection Process: The material is heated until it becomes molten, then injected into the mold cavity under pressure.
- Cooling Phase: The molten material cools and solidifies inside the mold.
- Demolding: Once cooled, the mold opens, and the final product is ejected.
Key Advantages of Choosing Custom Injection Molding
Partnering with custom injection molding companies brings several benefits to businesses engaged in manufacturing. Here are some of the most compelling reasons to consider this method:
1. High Efficiency and Productivity
Injection molding is designed for high-volume production. Once the mold is created, the process can be repeated countless times, allowing businesses to meet large order demands quickly and efficiently.
2. Exceptional Precision
The accuracy of molds ensures that the products produced meet stringent specifications. This precision reduces waste and rework, enhancing overall productivity.
3. Versatile Material Options
Custom injection molding can utilize a wide range of materials, including various plastics and even metals in some cases. This versatility allows companies to produce products that meet specific physical and chemical requirements.
4. Cost-Effective for Large Runs
While the initial design and fabrication of molds can be costly, the per-unit cost significantly decreases with larger production runs. Thus, the process becomes exceedingly cost-effective in mass production scenarios.
Choosing the Right Custom Injection Molding Company
Selecting the right partner for your injection molding needs is crucial for achieving high-quality results. Here are several factors to consider when choosing custom injection molding companies:
1. Industry Experience
Look for companies with a proven track record in your specific industry. Their understanding of industry-specific challenges and requirements can be invaluable.
2. Technology and Equipment
Modern equipment and cutting-edge technology are essential components that contribute to the efficiency and quality of the production process. Ensure the company stays up-to-date with advancements in their field.
3. Quality Control Measures
Inquire about their quality assurance processes. A reliable company will have stringent quality control measures to ensure that every part meets the required standards.
4. Customer Support and Communication
Effective communication is vital throughout the manufacturing process. Choose a company that offers responsive customer support and keeps you informed at every step.
5. Flexibility and Scalability
Ensure that the company can adapt to changes in production volume and product requirements. Scalability is critical as your business grows and evolves.
Applications of Custom Injection Molding
Custom injection molding is used in a vast array of industries, including:
- Automotive: Components such as dashboards, handles, and interior fittings are frequently produced using injection molding.
- Consumer Electronics: Mobile phone cases, laptop keys, and various other electronic components benefit from the precision of injection molds.
- Medical Devices: Many medical applications require high levels of precision and sterility, making injection molding an ideal choice.
- Toys: The toy industry relies on custom injection molding to create intricate designs and colorful products efficiently.
- Packaging: Custom molds are used for producing containers, caps, and other packaging solutions.
The Future of Custom Injection Molding
As technology continues to evolve, the future of custom injection molding companies looks promising. Significant trends to watch include:
1. Sustainable Practices
Businesses are increasingly focused on sustainability. Many injection molding companies are adopting eco-friendly materials and practices, such as reducing waste and energy consumption.
2. Industry 4.0
The integration of smart technology and automation into the injection molding process is enhancing efficiency and accuracy. Companies that adopt these technologies will likely maintain a competitive edge.
3. Advanced Materials
Innovative materials, such as biodegradable plastics and composites, are becoming more prevalent, offering new possibilities for manufacturers seeking sustainable solutions.
4. Customization and Personalization
As consumers demand more personalized products, injection molding companies are increasingly providing customization options, allowing businesses to meet specific customer needs.
Conclusion
In conclusion, custom injection molding companies play a crucial role in modern manufacturing, enabling businesses to produce high-quality, complex parts efficiently. By understanding the benefits, applications, and trends in this field, companies can make informed decisions when Partnering with an injection molding manufacturer. As the industry continues to evolve, staying updated with the latest technologies and practices will be essential for maintaining a competitive advantage.
To find a reliable partner for your injection molding needs, consider evaluating companies that align with your operational goals and values. A well-chosen partner can contribute significantly to your business's success and sustainability in the long term.