The Impact of Rapid Prototyping on Metal Fabrication
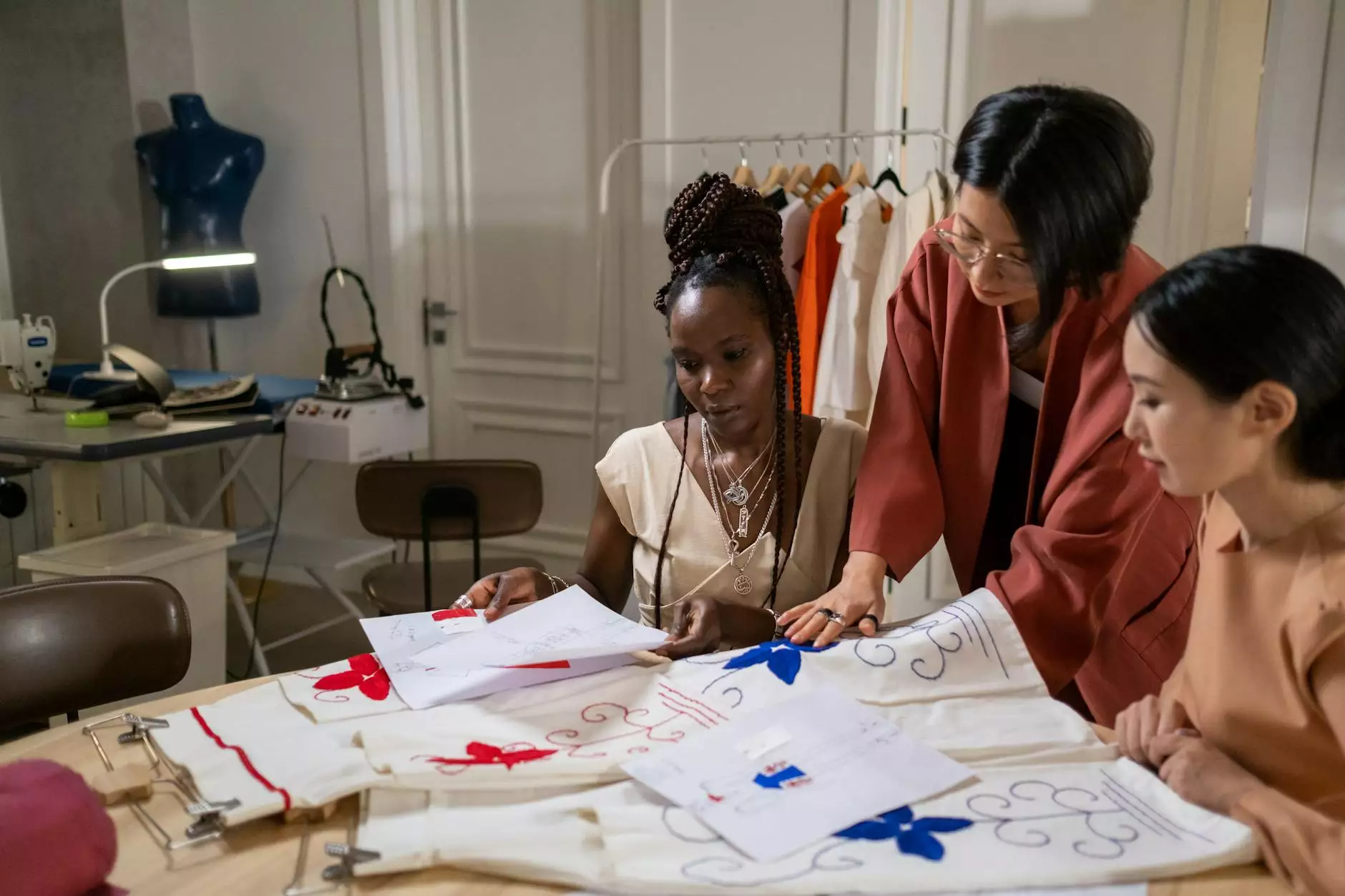
In the dynamic world of manufacturing, innovation is key to staying ahead of the competition. In recent years, the emergence of rapid prototyping has fundamentally changed the landscape of metal fabrication. This article delves into the nuances of rapid prototyping, exploring its significance, the technologies involved, and its transformative effects on the metal fabrication industry. we also discuss how businesses like DeepMould leverage these innovations to deliver exceptional products.
What is Rapid Prototyping?
Rapid prototyping refers to a group of techniques used to quickly fabricate a scale model of a physical part or assembly. The process takes a computer-aided design (CAD) file and transforms it into a physical object using a variety of tools and methods. This allows for rapid iterations, enabling businesses to refine their product designs swiftly. Common rapid prototyping methods include:
- 3D Printing: Utilizes additive manufacturing techniques to create objects layer by layer.
- CNC Machining: Involves the use of computer-controlled machines to cut and shape metal with precision.
- SLA (Stereolithography): A method that uses a laser to cure resin into solid plastic.
- SLS (Selective Laser Sintering): A process that uses a focused laser to fuse powdered material into solid parts.
The Importance of Rapid Prototyping in Metal Fabrication
Metal fabrication involves numerous steps, from design to production. Incorporating rapid prototyping into this process offers several key advantages that enhance efficiency and product quality:
1. Accelerated Design Process
The traditional method of product design and development can be time-consuming, often taking months or even years. With rapid prototyping, companies can reduce the time to market significantly. By producing prototypes quickly, designers and engineers can test and iterate on their ideas without lengthy delays.
2. Improved Accuracy and Precision
Another major benefit of rapid prototyping is the enhanced accuracy it brings to the fabrication process. Traditional methods can introduce errors during product creation; however, the precise technology employed in rapid prototyping minimizes these risks, ensuring that the final product matches the design specifications closely.
3. Cost-Effective Solutions
In many cases, the cost associated with prototyping can deter businesses from pursuing innovative designs. Rapid prototyping addresses this issue by reducing material waste and the time required for production. Moreover, using advanced digital technologies means that fewer physical prototypes are needed, further driving down costs.
4. Enhanced Collaboration
Rapid prototyping enhances collaboration among teams by providing physical models that can be easily shared and discussed. Visualizing a design helps stakeholders – from engineers to marketing teams – to understand a product better, fostering a collaborative environment that encourages innovation.
Key Technologies Driving Rapid Prototyping
The evolution of rapid prototyping has been underpinned by several advanced technologies, each contributing uniquely to the metal fabrication process:
1. Additive Manufacturing
The most notable technology associated with rapid prototyping is additive manufacturing, often synonymous with 3D printing. This method builds objects layer by layer, allowing for the creation of complex geometries that would be impossible or highly impractical with traditional techniques.
2. Computer Numerical Control (CNC) Machining
CNC machining is integral in prototyping, particularly for metal components. This technology ensures high precision and repeatability, making it an ideal choice for creating prototypes that require tight tolerances.
3. Digital Twin Technology
Digital twin technology creates virtual simulations of physical assets. By using real-time data, engineers can assess and optimize prototypes in a virtual environment before producing the physical model, leading to more informed decision-making.
The Step-by-Step Process of Rapid Prototyping
Implementing rapid prototyping in metal fabrication involves several critical steps:
Step 1: Concept Development
The process begins with the development of a concept. Designers brainstorm ideas and create initial sketches. This stage is vital for visualizing the end product.
Step 2: CAD Modeling
Once a concept is selected, a detailed CAD model is created. This model serves as the blueprint for the prototype and should include all necessary dimensions and specifications.
Step 3: Prototyping
The CAD model is then transformed into a physical prototype using one of the aforementioned methods. Here, the choice of materials plays a crucial role in determining the prototype’s functionality and durability.
Step 4: Testing and Evaluation
After the prototype is produced, rigorous testing is conducted. Feedback is gathered from stakeholders to assess performance, identify flaws, and suggest improvements.
Step 5: Iteration
The insights from testing lead to iterations on the design, refined through an ongoing cycle of prototyping and evaluation. This process ensures that the final product meets all necessary standards before proceeding to mass production.
Applications of Rapid Prototyping in Metal Fabrication
The applications of rapid prototyping in metal fabrication are vast and varied, impacting numerous sectors:
1. Aerospace Industry
In aerospace, lightweight and durable components are crucial. Rapid prototyping enables the creation of complex parts that reduce weight without sacrificing strength, ultimately leading to improved fuel efficiency and performance.
2. Automotive Sector
Automakers rely on rapid prototyping to accelerate their design processes. Creating prototypes of engine components, chassis, and consumer interfaces allows for quick testing and refinement before actual production.
3. Medical Devices
In the medical sector, precision is paramount. Rapid prototyping facilitates the design of custom implants, surgical instruments, and patient-specific solutions that enhance overall healthcare outcomes.
4. Consumer Products
Rapid prototyping is increasingly used in consumer product design, where speed and innovation can significantly impact market share. Designers can test ergonomics, aesthetics, and functionality before launching a product.
Future Trends in Rapid Prototyping
The future of rapid prototyping continues to evolve with advancements in technology. Some emerging trends include:
1. Integration with Artificial Intelligence
AI is expected to play a significant role in optimizing designs and analyzing data from prototypes. This integration will lead to smarter manufacturing processes and more intricate designs.
2. Sustainability Practices
As industries strive for sustainability, the materials used in rapid prototyping are becoming increasingly eco-friendly. Innovations in biodegradable materials and recycling processes are paving the way for greener manufacturing methods.
3. Enhanced Customization
With growing consumer demand for personalized products, rapid prototyping technologies are enabling an unprecedented level of customization that caters to individual preferences and needs.
Conclusion: The Future of Metal Fabrication with Rapid Prototyping
Rapid prototyping is not merely a trend; it is a fundamental shift in how metal fabrication operates. By embracing this innovative approach, businesses like DeepMould position themselves at the forefront of manufacturing excellence. With the ability to design, test, and produce efficiently, the future of metal fabrication is brighter than ever. Companies that harness the power of rapid prototyping will undoubtedly lead the way in producing high-quality, precision-engineered products that meet the ever-changing demands of the market.
rapid prototyper