Ultimate Guide to Injection Moulding Tool Design
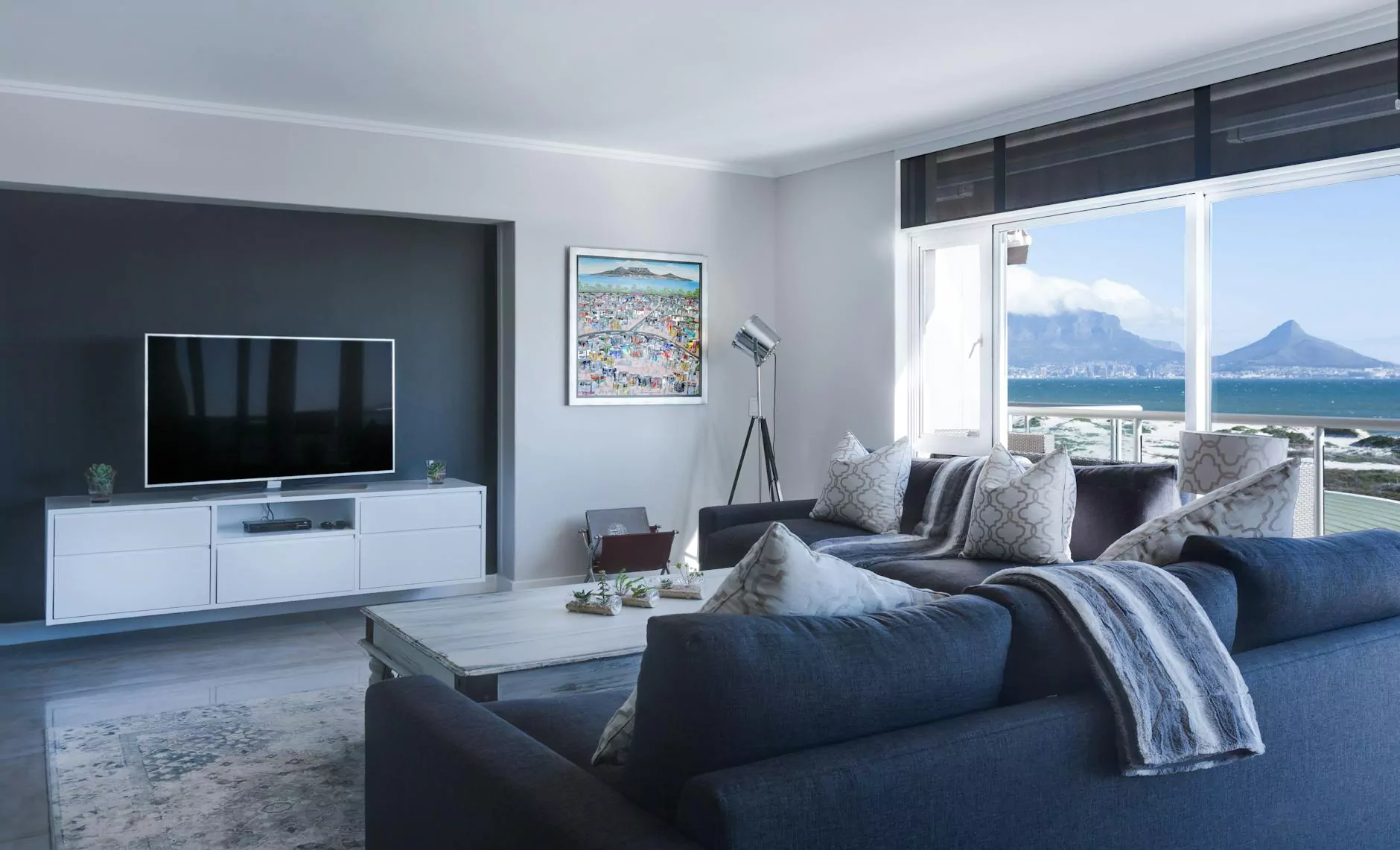
The world of manufacturing is continuously evolving, and at the heart of many production techniques lies the process of injection moulding tool design. This intricate art is fundamental for creating consistent, high-quality products across various industries, especially within metal fabrication. In this comprehensive guide, we’ll delve deep into the principles, processes, and benefits of effective injection moulding tool design, showcasing how it can elevate your business and streamline operations.
Understanding Injection Moulding
Injection moulding is a manufacturing process where molten material is injected into a mould to create specific parts or products. This technique is pivotal in industries that require the production of detailed and complex items, from consumer goods to automotive components. The success of this process greatly depends on the quality of the injection moulding tool design.
What is Injection Moulding Tool Design?
Injection moulding tool design refers to the careful engineering and planning involved in creating the moulds used in the injection moulding process. This includes the design of the mould itself, the choice of materials, and the configuration that affects cooling times and production efficiency. A well-executed tool design ensures that the final products meet precise specifications and exhibit superior quality.
The Importance of Quality Tool Design
The significance of effective injection moulding tool design cannot be overstated. Here are several key reasons why:
- Precision and Accuracy: A well-designed mould guarantees that the dimensions and tolerances of the final product are met consistently.
- Reduced Production Costs: High-quality mould designs minimize material waste and increase the lifespan of the mould, leading to lower overall production costs.
- Enhanced Product Quality: With precise tooling, the final products exhibit excellent surface finish and dimensional accuracy, which is critical for customer satisfaction.
- Improved Efficiency: Efficient mould designs allow for faster cycle times, thus increasing overall productivity.
Key Elements of Injection Moulding Tool Design
Understanding the critical components of injection moulding tool design is essential for achieving optimal results. Here are the fundamental elements:
1. Material Selection
The choice of materials for both the mould and the product is pivotal. High-quality steel or aluminum is often used for moulds because of their durability and resistance to wear. The material of the product must also be considered, as it will affect the design parameters, processing temperature, and cooling time.
2. Mould Configuration
Tool designers must consider the shape and complexity of the product. This includes ensuring that the mould can be fabricated effectively and will allow for necessary cooling channels for efficient thermal management. Design features such as draft angles, wall thickness, and gate locations must be meticulously planned.
3. Cooling Systems
Efficient cooling systems are essential to reduce cycle time and ensure uniform temperature distribution. The incorporation of features such as conformal cooling channels can significantly improve the cooling efficiency, resulting in better quality outputs and reduced warping.
4. Ejection Mechanism
An effective ejection mechanism is crucial for the smooth retrieval of the molded parts from the mould. This could include ejector pins, plates, or other systems designed to release the part without causing damage.
Steps in the Injection Moulding Tool Design Process
Embarking on the journey of injection moulding tool design involves several key steps:
- Concept Development: Engage with stakeholders to outline the product requirements and desired specifications.
- 3D Modelling: Utilize advanced CAD software to create a digital representation of the mould. This stage allows for visualizing the design and making necessary adjustments.
- Prototyping: Often, a prototype mould is created using rapid prototyping techniques to test and refine the design before final production.
- Testing and Validation: The prototype undergoes rigorous testing to identify any issues or areas for improvement.
- Final Production: Following successful testing, the final mould is produced, taking into account all adjustments made during prototyping.
Technological Advances in Injection Moulding Tool Design
As technology continues to advance, several innovations have significantly impacted injection moulding tool design:
1. Computer-Aided Design (CAD)
CAD technology has revolutionized how molds are designed, allowing for intricate designs that would be impossible to create manually. CAD enables precise measurements, 3D visualizations, and quick adjustments, drastically reducing design time.
2. Computer-Aided Manufacturing (CAM)
CAM integrates with CAD to facilitate the manufacturing process, enabling automated machining of mould components. This results in higher precision and improved consistency in the production process.
3. Additive Manufacturing
The introduction of 3D printing technologies allows for rapid prototyping and even production of certain mould components. This accelerates the design process and minimizes costs associated with traditional manufacturing methods.
4. Simulation Software
Advanced simulation tools allow designers to visualize fluid dynamics, thermal characteristics, and stress points within the mould, enhancing the efficiency and effectiveness of the design before it is physically created.
Challenges in Injection Moulding Tool Design
Despite its advantages, injection moulding tool design does face certain challenges:
- High Initial Costs: The investment in high-quality moulds can be costly, particularly for complex designs.
- Design Complexity: Intricate designs may complicate the manufacturing process and require specialized tools or techniques.
- Material Limitations: Certain materials may not perform well in injection moulding due to their properties, necessitating thoughtful material selection.
- Maintaining Precision: Over time, moulds can wear down, affecting their precision and leading to increased scrap rates if not properly managed.
Best Practices for Effective Injection Moulding Tool Design
To ensure that your injection moulding tool design is successful, consider the following best practices:
- Collaborate with Experts: Engage with experienced engineers and designers who specialize in injection moulding.
- Invest in Training: Keep your design team updated with the latest tools, technologies, and best practices in the industry.
- Emphasize Prototyping: Develop prototypes early in the design process to identify and rectify potential issues before full-scale production.
- Continuously Evaluate: After production has commenced, consistently evaluate the design for improvements based on product performance data.
The Future of Injection Moulding Tool Design
The injection moulding industry is poised for exciting developments as technology continues to evolve. Increasingly, AI and machine learning are being integrated into both the design and production processes, allowing for predictive maintenance and optimized production schedules. Moreover, the emphasis on sustainability means that designers will need to think critically about material selection and waste reduction strategies.
Conclusion
In conclusion, effective injection moulding tool design is essential for any manufacturer looking to excel in today’s competitive marketplace. By understanding the principles of tool design, leveraging new technologies, and adhering to best practices, businesses can create high-quality products that meet customers' needs and stand out in the industry. As you develop your injection moulding processes, remember that the quality of your tooling directly impacts your success—prioritize it, and reap the benefits in both efficiency and product quality.
For more expert insights and professional services in metal fabrication and injection moulding tool design, visit deepmould.net.